他の人がバラシ終わった図面を検図する時に、「この程度の図面不備は自己検図でつぶして欲しいなぁ」と思う事ありませんか?
例えば次のような単純なミスです。
・寸法が抜けている
・タップ穴なのにバカ穴指示になっている
・材質がおかしい
・相手部品と干渉している
・購入品の取り付け穴が合っていない
このような図面不備は製図者自身で自己検図でつぶしてから検図をお願いするのが良いと思います。
図面の不備箇所の修正依頼をするのも手間がかかるし、修正箇所が多すぎると「指示出すくらいなら自分で直してしまえ」となり検図者の負荷が増えてしまいます。しかも当の製図者側から考えても、修正指示が無い=バラシに問題が無かった、となってしまいミスに気付かず成長もできなくなってしまいます。
しかし図面の検図って慣れるまでに時間がかかるうえに、検図のやり方を教えてもらおうにも人それぞれ手順が違っていてこれといった正解がありません。なんとなく見様見真似で部品寸法とか購入品の型式とかを確認して~という人が多いと思います。そもそも自己検図が必要という認識が無い人もいるかもしれません。
実際私も検図のやり方を教えてもらった記憶はあまりなく、図面の不備が発覚してから「ここのチェックが甘かったのかぁ」と反省しながら徐々に検図の経験を積んできました。
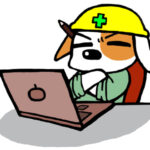
図面の検図方法のマニュアル的なものが少しでもあれば良かったのになぁ
そこで本記事では設計者が思う「ここまでは自己検図をして欲しい!」と題して、自己検図の方法を「手順1は~、手順2は~」のように順序立てて解説していきます。設計初心者の方はぜひ目を通してみてください。
※ここで紹介するのは「部品図のバラシ」に焦点を当てての検図方法です。機能を満たしているか?仕様漏れは無いか?強度は大丈夫か?メンテナンス性は?などの機能的な確認は3Dの段階でするべきだし、解説もかなり難しいので本記事の検図方法からは対象外としています。
効率良く検図するための確認順序
検図は正確かつ効率良く進める必要があります。
効率を良くするポイントは人それぞれ違うと思いますが、私は”確認する目線をぶれさせない”ことが大事だと考えます。
例として効率の悪いor良い検図を10枚の図面の場合で説明すると、それぞれこんなイメージになります。
1枚の図面に対し、全寸法を確認→材質や表面処理の確認→製図者の記載の確認→組付けに問題ないかの確認をして、それを2枚目、3枚目と順に確認していくような”部品図1枚ずつを完成させていく検図”
確認する項目を決めて、その項目を10枚通して確認していく検図方法。1つ目の確認項目が終われば次の確認項目を再度10枚通しで確認していき、これを確認項目の数だけ繰り返すような”全部品図の完成度を同時に上げていく検図”
1枚ずつ検図していく方法だと、寸法を確認するのか?または材質を確認するのか?といった”確認する目線”が図面ごとに行ったり来たりして、うっかりミスが起きやすくなります。図面間の整合もとりづらいです。
逆に1つの項目の確認のみの目線で検図していくと、寸法なら寸法!材質なら材質!といった具合に目線を固定できるので、全部の図面を最後まで通しで集中して検図できます。
何度検図してもその度に抜けが発覚してしまう場合はこの”効率の悪い検図”をしているかもしれないので注意してみてください。
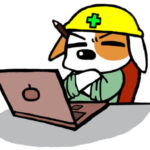
あくまでも個人的にそう感じているだけなので、1枚ずつ仕上げていくやり方のほうが良いという人もいると思います。その人のやり方を批判しているわけではありませんので、ご了承いただければと思います。
次項からは実際に見るべきポイントを手順に沿って説明していきます。
手順.1「加工ができる図面か」に対しての確認
まずは一番重要な”加工ができる図面か?”を確認します。寸法抜けや材質などの図枠情報が間違っていては加工ができないので、そこに対しての確認になります。
1-1. 外形寸法
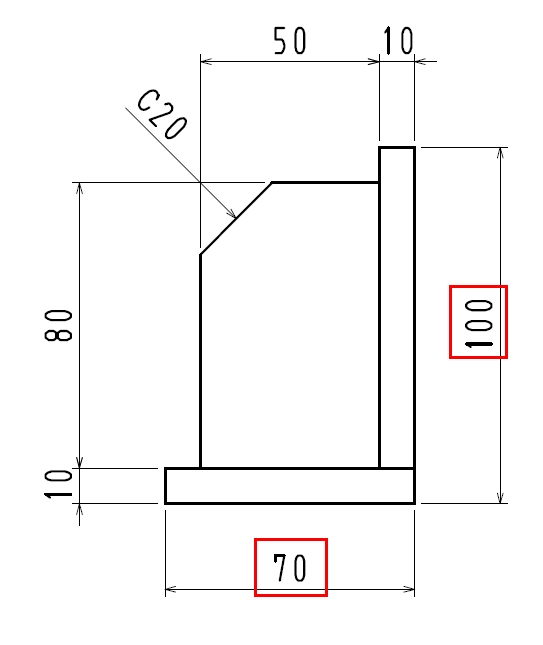
まずは外形寸法を確認しましょう。
穴寸法や公差など細かい寸法がバッチリ書かれていても、外形寸法が抜けている図面をまれに見ます。
恐らく重要そうな寸法に気を取られて、単純な外形寸法を忘れてしまうんだと思います。
1-2. 素材寸法
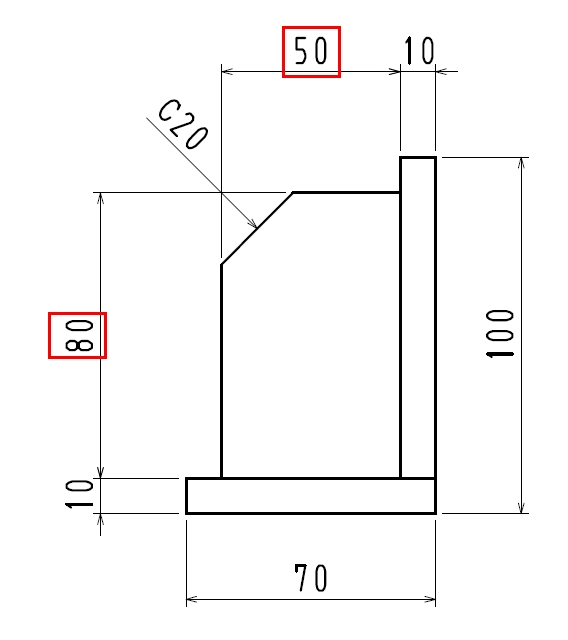
単純な切削加工でできる部品は「素材寸法=外形」ですが、溶接部品の場合には注意が必要です。
例えばリブを溶接する部品の場合は、「リブの素材寸法がキチンと記載されてるか」を確認します。
特に複数の部品の溶接からなる製缶部品だと、寸法線が多くなり忘れやすいです。1個ずつ素材寸法が抜けていないか確認しましょう。
外形寸法にも言えることですが、一番最初に入れる寸法を素材寸法にしてしまえば寸法抜けが発生しづらくなります。抜けの多い方は意識してみてください。
1-3. 穴の位置、数量、径の寸法
穴に関しては位置、数量、径をまとめて確認するのが効率が良いです。
以下が要チェックポイントです。
1-4. 仕上げ面(表面粗さ)
部品が取り付く面はある程度きれいに仕上げる必要があります。
素材のままでOKな面、研削で仕上げる面、または手仕上げが必要な面など、使用方法に適した表面粗さが記入されているか確認しましょう。
精度が必要な部品は仕上げ面を寸法の基準にする場合もあるので要注意です。
1-5. 面取り
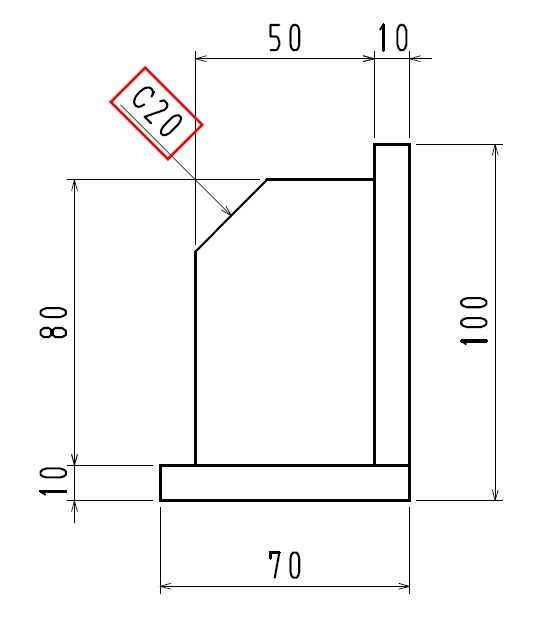
面取りは最後に記入することが多いので忘れやすいポイントの一つです。
面取りの大きさと数量に間違いが無いか確認しましょう。他の寸法線に被ってないかも要確認です。
1-6. 図枠情報の確認
図枠で重要なのが”部品数量、材質、表面処理”あたりで、次いでマシン名、ユニット名、製図者、日付などになります。会社によっては図枠内に表粗さを入れていることもあるので、合わせて問題ないか確認しましょう。
図枠での失敗で多いのが「別の図面からコピーしてきた図枠の中身を変え忘れていた」という失敗です。部品名程度の間違いならまだマシですが、焼き入れ指示が抜けていたり、架台の塗装色を間違えてしまうと取り返しがつかなくなってしまいます。
また対象部品の確認も必須です。
本当は本形状2個、対象形状2個必要なのに、気付かずに数量に4と書いてしまう図面をよく見ます。
これは本来3Dモデルの段階でコメントなどで対象であることの情報を付加して、バラシ作業者がぱっと見で気付けるようにする必要がありますが、なかなかそうではないのでバラシ作業者が必ず確認しましょう。
手順2.「組付けに問題ないか」に対しての確認
加工図面として問題ないことが確認できたら、次は部品を組み上げていくことを想定した検図をします。この検図では部品図を単体ではなく複数枚同時に確認することになります。
代表的な確認項目は”取付穴、購入品の取付、部品同士の干渉”になります。
2-1. 取り付け穴確認
「ボルトと穴の径が正しいか」、「両方の部品とも穴ピッチは同じか」、「穴の空け忘れはないか」を主に確認していきます。
穴ピッチを変更した際に相手部品の修正をし忘れていることは割と起こるので、3D断面図や部品を透過させる機能を利用したりして確認しましょう。
2-2. 購入品の確認
購入品との取り付け関係を確認します。この時に注意したいのが、購入品は3Dモデルではなく”カタログの寸法”で確認するということです。
購入品の3Dモデルは各メーカーからダウンロードして使用しますが、まれにモデルが間違っていることがあります。
またメーカーの3Dモデルは穴径が統一されていないので勘違いが起こりやすいです。M5タップ穴で例えると、谷径のφ4.134で表示されるものもあればφ5で表示されているものもあります。φ5の場合はもしかしてタップ穴ではなく公差穴かもしれません。これらは3Dモデルだけでは確実な判別はできません。
いちいちカタログを見るのは面倒ですが、その手間は必要な手間なので面倒くさがらずに確認しましょう。もしカタログを設計中でダウンロードしていたならば、そのタイミングでPCに保存しておき検図者に図面と一緒に渡すと効率が良いですね。
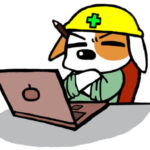
最近は間違った3Dモデルはあまり見かけませんが、穴径の勘違い防ぐためにもカタログ値を確認しましょう。
2-3. 干渉確認
部品同士の干渉確認をします。ほとんどの3DCADには干渉確認機能が備わっているのでそれを利用して確認します。
動作する箇所は原点位置、移動後位置それぞれで確認しましょう。(動作させながら干渉確認できれば完璧なのですが、CADではなかなか難しいのでそこは頭の中で動作を仮想して確認しましょう。)
もし干渉確認機能は動作が重い場合は、小分けにアセンブリごとに切り分け複数回に分けて実施する方法をとりましょう。
手順3.「過去の製作実績との整合性」に対しての確認
これは参考とする図面がある場合の確認項目になりますが、参考図面との整合性も確認する必要があります。
ざっと思いつくのが以下の内容で、会社によってルールで定められていることもあるので要注意です。
検図のまえに参考図面をザーっと一通り目を通しておけば「どんな取り決めがありそうか」がある程度把握できます。
まとめ
まとめると、効率の良い自己検図方法は以下の通りです。
手順.1「加工ができる図面か」に対しての確認
手順2.「組付けに問題ないか」に対しての確認
手順3.「過去の製作実績との整合性」に対しての確認
検図には時間をかけましょう。私の場合ざっくりですが、バラシ時間の半分の時間を検図にかけることもあります。バラシに2日かかったとしたら検図に1日かけてる感じですね。
納期との兼ね合いもありますが、可能な限り隅々まで検図しましょう。
コメント